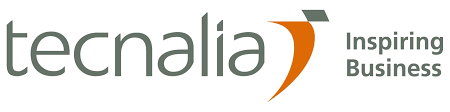
TECNALIA es el mayor centro de investigación aplicada y desarrollo tecnológico del estado, un referente en Europa y miembro de Basque Research and Technology Alliance. Colaboramos con las empresas e instituciones para mejorar su competitividad, la calidad de vida de las personas y lograr un crecimiento sostenible. Nuestra Misión: Transformar investigación tecnológica en prosperidad. Nuestra Visión: Ser agentes de transformación de las empresas y de la sociedad para su adaptación a los retos de un futuro en continua evolución. Somos la primera organización privada de España en contratación, participación y liderazgo en el programa Horizon 2020 de la Comisión Europea y la tercera en solicitud de patentes europeas. Conoce nuestra actividad en robótica con estos videos cortos : 2021 : https://youtu.be/UMIcb_h08mQ 2020 : https://youtu.be/n8H4Dx8mYvQ https://www.tecnalia.com/en/infrastructure/flexible-and-collaborative-robotics-laboratory
Entity type: Research and/or Technological Centre
Size: > 200
State: Gipuzkoa
Country: Euskadi
Contact: Jon Agirre Ibarbia (jon.agirre@tecnalia.com)
Web: https://www.tecnalia.com/
Type of tecnology base of the institution activities
- Agriculture
- Healthcare
- Industrial robotics
- Logistics and transport
- Construction
- Laboratory Robotics
- Maintenance and Inspection
- Marine Robotics
- Aerial Robotics
- Wearable Robotics
- Safety
- AI and Cognition
- Autonomous Navigation
- Mechatronics
- Software Engineering, Systems Integration and Systems Engineering
- Perception
- Telerobotics and Teleoperation
- Cloud Robotics
- Cybersecurity
- Entrepreneurship
Types of activities developed by the institution
- Development and manufacturing of robotic equipment and technologies for end
- Robot programming (software development)
- Integral customised projects for end users
- Research and development projects
Project 1
Name: SHERLOCK (H2020-FOF). 2019-2022 : Seamless and safe human-centred robotic applications for novel collaborative workplacesWeb: https://sherlock-project.eu/
Summary:
It promotes the safe and efficient collaboration between humans and soft robots by introducing cognitive capabilities that will allow the robots to detect the human, understand his/her intentions and seamlessly collaborate for the execution of production tasks. The project starts from a basis where safety is already guaranteed using safe robotics that the partners have brought to market in previous projects.
Funding source: Yes
Funded externally: Yes
Developed in consortium: Yes
Project 2
Name: VERSATILE (H2020-ICT) 2017-2019 : Innovative robotic applications for highly reconfigurable production linesSummary:
Objective: to provide a bridge for transferring, demonstrating and validating the latest R&D results in robotics towards different industrial environments proving their applicability and effectiveness. More specifically, VERSATILE will apply dual arm robots in executing complex tasks that are traditionally assigned to humans due to their manipulation requirements
Funding source: Yes
Funded externally: Yes
Developed in consortium: Yes
Project 3
Name: THOMAS (H2020-FOF) 2016-2020 : Mobile dual arm robotic workers with embedded cognition for hybrid and dynamically reconfigurable manufacturing systemsWeb: http://www.thomas-project.eu/
Summary:
Aims at creating a dynamically reconfigurable shopfloor utilizing autonomous, mobile dual arm robots that are able to perceive their environment and through reasoning, cooperate with each other and with other production resources including human operators. THOMAS will demonstrate and validate its developments in the automotive and the aeronautics industrial sectors.
Funding source: Yes
Funded externally: Yes
Developed in consortium: Yes
Project 4
Name: SARAFUN (H2020-ICT) 2015-2017 : Smart Assembly Robot with Advanced FUNctionalitiesWeb: https://sarafun.eu/
Summary:
Objective: to enable a non-expert user to integrate a new bi-manual assembly task on a robot in less than a day (by augmenting the robot with cutting edge sensory and cognitive abilities).TECNALIA: development of instrumented tools limiting the sensory feedback and dexterity of the fingers to that of the target robotic system and providing key information about the gestures and applied force performed by the human.
Funding source: Yes
Funded externally: Yes
Developed in consortium: Yes
Project 5
Name: TRACEBOT (H2020-ICT) 2021-2025 : Traceable Robotic Handling of Sterile Medical ProductsWeb: https://www.tracebot.eu/
Summary:
TraceBot project aims at addressing healthcare-related processes, and more exactly the membrane-based sterility testing process. The objective of TraceBot is to bring verifiable actions to robot manipulation by reasoning over sensor-actor trails in a traceability framework based on digital-twin technology and extend current robot motion planners with the automatic execution of self-checking procedures that create a semantic trace of the actions performed. The goal is to create robotic systems able to understand what they perceive and do, to ensure that any manipulation action is verified, thus meeting the needs of the regulated environment.
Funding source: Yes
Funded externally: Yes
Developed in consortium: Yes
Project 6
Name: HEPHAESTUS (H2020-ICT) 2017-2020 : Highly automatEd PHysical Achievements and PerformancES using cable roboTs Unique SystemsWeb: https://www.hephaestus-project.eu/
Summary:
The HEPHAESTUS project explores the innovative use of robots and autonomous systems in construction, a field where the incidence of such technologies is minor to non-existent. The project aims to increase market readiness and acceptance of key developments in cable robots and curtain walls. Over the project lifetime it shall produce fundamental technical validation outside the lab, and deliver significant results such as:a prototype cable robot, designed to build, repair and maintain a building façade; a prototype building and curtain wall system, suitable for robot assembly; and a business plan for widespread commercial adoption.
Funding source: Yes
Funded externally: Yes
Developed in consortium: Yes
Project 7
Name: MAELSTROM (H2020-FNR) 2021 - 2024 : Smart technology for MArinE Litter SusTainable RemOval and ManagementWeb: https://www.maelstrom-h2020.eu/
Summary:
The global marine plastic litter challenge comprises an estimated stock of 83 million tonnes of plastic waste accumulated in oceans. The recovery of plastic materials already in the ocean is an arduous and costly task. The EU-funded MAELSTROM project is bringing together key stakeholders – from research centres and recycling companies to marine scientists and robotic experts – to leverage the integration of complementary technologies for the sustainable removal of marine litter in different European coastal ecosystems. The project will design, manufacture and integrate scalable, replicable and automated technologies, co-powered with renewable energy and second-generation fuel, to identify, remove, sort and recycle all types of collected marine litter into valuable raw materials. The underwater cable robot will be developed by TECNALIA and CNRS-LIRMM as an upgrade of the COGIRO cable robots used in industrial plants that will be adapted to the MAELSTROM marine underwater activities.
Funding source: Yes
Funded externally: Yes
Developed in consortium: Yes
Project 8
Name: CableBOT (FP7-FoF) 2011 - 2014 : Parallel Cable Robotics for Improving Maintenance and Logistics of Large-Scale ProductsWeb: https://www.cablebot.eu/en/
Summary:
The CableBOT project deals with a novel methodology for designing, developing and evaluating cable robots customised for the automation in large-scale auxiliary processes. Parallel cable robots extend the payloads and workspace of conventional industrial robots by more than two orders of magnitude. The main objective is to develop a new generation of modular and reconfigurable robots able to perform many different steps in the post-production of large-scale structures. Two application examples are targeted in close cooperation to industry: aeronautical applications of maintenance (EADS) and the handling of construction beams (ACCIONA). Benefits include an increase of production efficiency, a wider range of products, light and reconfigurable structure mechanisms and adaptable and more flexible operator assistance systems.
Funding source: Yes
Funded externally: Yes
Developed in consortium: Yes
Project 9
Name: REMODEL (H2020-FoF) 2019 - 2023 : Robotic tEchnologies for the Manipulation of cOmplex DeformablE Linear objectsWeb: https://www.remodel-project.eu//
Summary:
The factory of the future will be fully automated. Right now, robotics have yet to replace all types of manual labour, particularly complicated tasks that involve the handling of complex materials and objects. Deploying robots for these tasks is necessary to ensure Europe can compete with countries having large labour forces. The EU-funded REMODEL project supports new production environments for manufacturing products with extensive wires and cables. It integrates a dual-arm robot in the production line for routing and fitting with advanced techniques. It will use the former WIRES project’s tools to solve electric wire manipulation issues, as well as add new perception and interaction functions. This will be tested for effectiveness in four industrial cases.
Funding source: Yes
Funded externally: Yes
Developed in consortium: Yes
Project 10
Name: CLEANDEM (H2020-Euratom) 2021 - 2024 : Cyber physicaL Equipment for unmAnned Nuclear DEcommissioning MeasurementsWeb: https://www.linkedin.com/company/cleandem-project/about/
Summary:
The European decommissioning and dismantling (D&D) market for nuclear facilities is characterised by significant long-term growth. The EU-funded CLEANDEM project will develop a technological breakthrough for D&D operations that will save time, reduce costs, and minimise human intervention while increasing safety. With the collaboration of 11 partners from 4 EU countries, the project will deliver a cyber-physical system using an unmanned ground vehicle platform equipped with innovative radiological sensing probes. It will conduct a radiological assessment of the area and monitor D&D operations. This will result in a 3D and fully detailed digital twin of the surveyed area augmented with radiological information.
Funding source: Yes
Funded externally: Yes
Developed in consortium: Yes